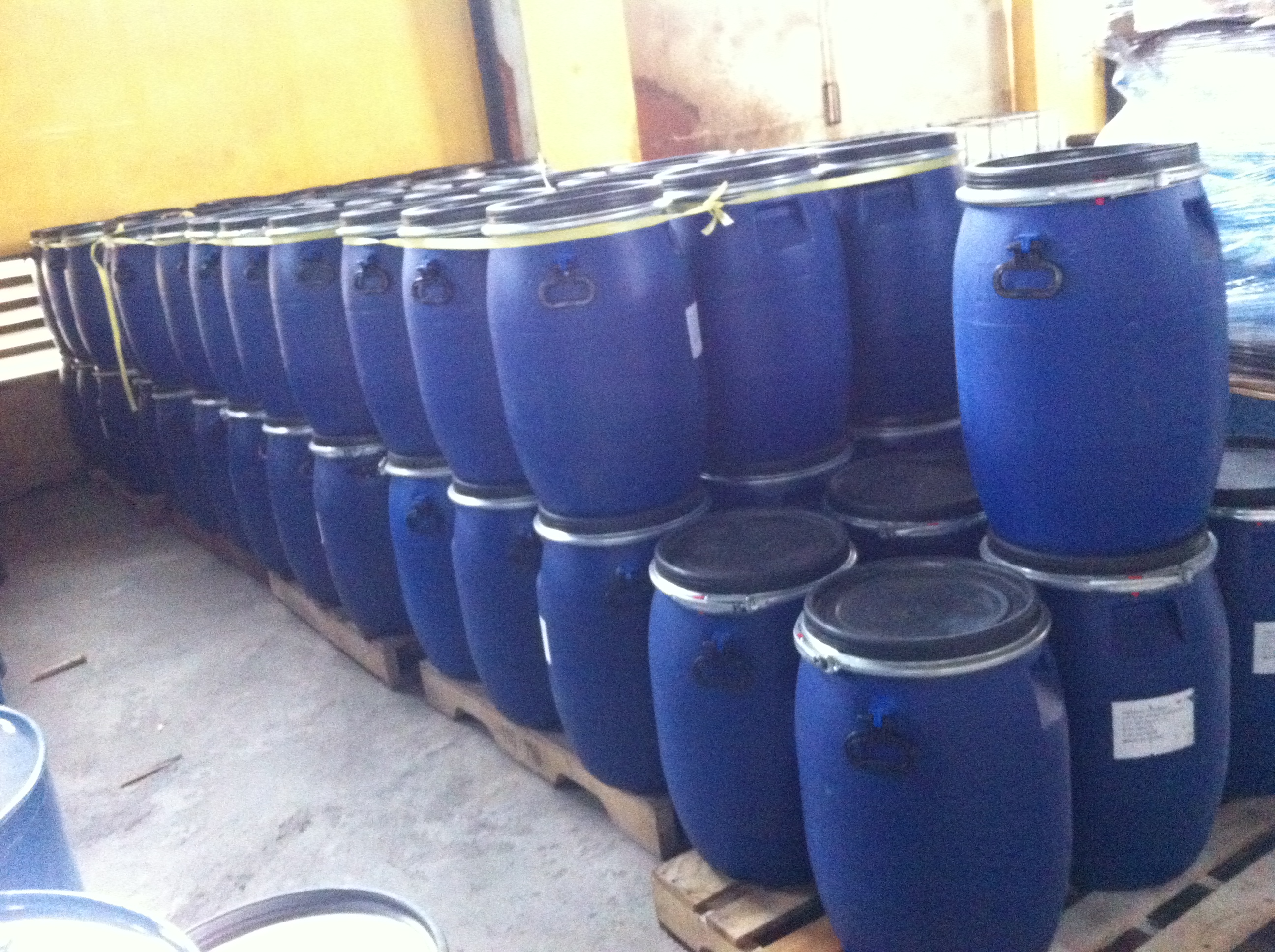
Afranil® MG
Chemical nature
Aqueous emulsion of a mixture of aliphatic
hydroxy compounds.
Physical form: white emulsion
Areas of appl icat ion
Defoamer and stock deaerator for the
pulp and paper industry
Afranil MG is supplied in the form of a
milky emulsion which is easy to dilute
with water. Afranil MG is a very effective
defoamer and deaerator for paper
stock. First and foremost, this defoamer
for low to medium temperatures can
promote the agglomeration of small air
bubbles and thereby improve deaeration
to a considerable extent. It is most
effective at temperatures between 30
and 45 °C.
No alkylphenol ethoxylates are used in
the production of Afranil MG.
Technical dat a
Solid content ca. 28 %
App.- viscosity 150 – 1500 mPa·s
pH value 6.5 – 9.5
Density approx. 0.96 g/cm³
For detailed information see Specification
Data Sheet
Appl icat ions
Afranil MG is a defoamer for low to
medium temperatures, i. e. it retains its
complete performance capability in the
low to medium temperature range between
30 and 45 °C.
A particular advantage of Afranil MG is
that it prevents hydrophobic substances
from collecting on the surface of the
stock due to flotation. It also prevents
foam from forming on the surface of the
white water in the drainage trays.
Afranil MG makes a great contribution
to keeping the whole white water system
free of undesirable substances.
The effectiveness of this product is
demonstrated by the fact that large
bubbles are initially formed, which then
quickly collapse. Any foam that does
form when waste paper is repulped
remains clean.
Afranil MG is also an effective stock
deaerator. Adding Afranil MG causes
the stock on the wire or in the cylinder
to drain more quickly, which gives rise
to improved formation. Web breaks are
less frequent, and there is a general
improvement in paper quality.
As little as 0.02 % and no more than
0.1 % Afranil MG, expressed as a proportion
of the stock, is sufficient to
deaerate it and prevent foam beingformed
at the surface.
The method by which Afranil MG is
metered into the stock can be adapted
to suit all circumstances. In work with
dilute emulsions the ratio of product to
water should not be less than 1 : 3.
It needs to be stirred well before use,
and
occasional gentle stirring helps prevent
dilute emulsions from creaming. We
have developed an automatic metering
plant for Afranil which offers a number
of practical advantages.
If Afranil MG is added to the white water
undiluted, it must be added at a point at
which the flow is sufficiently turbulent for
it to mix.
The emulsion can be metered direct
into the stock by means of diaphragm
pumps or piston pumps, but progressive
cavity pumps are more effective because
they do not pulsate. The rate
of flow can be measured with a magnetic
induction flowmeter. We would
recommend diluting it on-line with
100 – 200 l/h of water downstream of
the pump in a Lusap® static mixer.
Emptying of tankers:
It is advisable to use low-shear pumps
for discharging road tankers (see Recommendations
on use). Because the
last remaining portion of emulsion usually
has to be forced into the tank with a
large amount of air at the end of the
transfer procedure with compressed air,
severe foaming and the formation of
specks can occur. This must be avoided.
For this reason, it is advisable to fit
the filler pipe inside the tank in such a
way that the filler bend leads to the wall
of the tank above the maximum level of
liquid. The product can then run down
the wall and the air can escape without
bubbling through the liquid.
Storage:
Afranil MG should be protected
against direct sunlight and stored in
a place which is cool but free of
frost. Liquid that has been allowed
to freeze must be thoroughly homogenized
before use.
To prevent creaming, an Afranil
storage tank should be fitted with a
slowly rotating stirrer (20 – 50 rpm,
depending on the diameter of the
tank and the design of the stirrer). It
is sufficient to stir for about 5 minutes
every three days in order to
ensure complete mixing of the product.
Constant stirring is not recommended.
If there is no stirrer available to stir
the product, care must be taken to
ensure that, if a pump is used (see
Recommendations on use regarding
suitable pumps), no air is introduced
into the product, as it would cause
foam to form. The formation of foam
during feed operations must be
avoided and can be prevented by
allowing the product to run down the
tank wall or by feeding it back in
below the surface of the liquid. If
foaming occurs, there is always the
danger that larger agglomerates will
form. The pumping frequency
should be geared to the geometry of
the tank.
If the product is stored in IBCs,
creaming can become evident in the
form of a seemingly dark layer at the
bottom of the container. In this case
the product can be rehomogenized
by stirring; this will not impair the
effectiveness of the product.
Because Afranil MG, as an aqueous
emulsion, can dry up if left to stand
in an open container, the container
must always be closed again after
product has been taken out. Dry
remains of Afranil MG can be removed
very easily with hot water.
For storage tanks we recommend
an aeration and ventilation vessel.
Afranil storage tanks should be
cleaned at least every six months.
Based on our experience to date,
the following materials are suitable
for storage tanks, feed lines and
pumps:
High-grade steels:
Material No. 1.4541 [V2A]
Material No. 1.4571 [V4A] and
higher grade steels
Plastics: Polyethylene, polypropylene,
PVC, epoxy resin and GRP
tanks e. g. made of Palatal®
Bình luận
Chưa có bình luận nào!
Phản hồi
Bình luận từ Facebook